cttn-iren.com
En France, l’interdiction du perchloréthylène dans les pressings situés dans le voisinage de locaux occupés par des tiers (par exemple, en centre-ville ou galerie marchande), a engendré l’apparition sur le marché de plusieurs solvants alternatifs. Parmi eux, bien qu’ils soient tous différents dans leurs compositions exactes, plusieurs consistent en un mélange entre un hydrocarbure et un certain éther de propylène glycol, ou un alcool modifié dans un cas.
Ces composés ont bien sûr pour fonction de renforcer l’efficacité du solvant.

Dans un cycle de nettoyage à sec standard, le solvant souillé est filtré pour le débarrasser des matières
non-solubles et puis distillé, pour en séparer les matières solubles. Le distillat, sous forme de vapeur de solvant, passe sur un condenseur duquel il est envoyé en phase liquide dans un séparateur de phase.
En effet, à ce stade, les condensats de distillation peuvent contenir de l’eau. Pour recycler le solvant in situ
(but ultime de la filtration et de la distillation), il s’agit de le séparer de l’eau qu’il contient.
De même, les condensats issus du séchage sont également envoyés dans un séparateur de phase, qui peut être le même, ou bien distinct du premier. Le séchage consiste aussi en une évaporation du solvant
que contiennent les articles textiles après nettoyage (en plein bain ou par pulvérisation). Or, ces derniers renferment naturellement une certaine humidité lors de leur introduction en machine. De plus, les additifs que l’on est susceptible d’utiliser (prébrossant ou renforçateur de nettoyage, notamment), sont sous forme de solutions aqueuses. Le séchage a donc pour effet d’évaporer à la fois le solvant et aussi ces eaux, bien que présentes en quantités réduites.
Le ou les séparateurs permettent donc, par décantation du fait de la différence de densité entre l’eau et le
solvant, de séparer la phase aqueuse de la phase solvant. Cette dernière est réintroduite dans les réservoirs de la machine.
La phase aqueuse, dite « eau de contact », est ensuite éliminée. Or, il est impératif qu’elle ne contienne pas ou très peu de trace de solvant. On compte d’ailleurs sur une réutilisation maximum du solvant lors des cycles de nettoyage suivants, selon le principe d’une machine de nettoyage à sec.
Théoriquement, le procédé de nettoyage, répété encore et encore, permet la réutilisation du solvant en
cycle quasi-fermé.
Cependant, le phénomène de miscibilité des solvant alternatifs avec l’eau, en particulier la miscibilité des composés évoqués plus haut (relativement élevée) entraîne une perte de solvant via les eaux de contact.
Ainsi, le mélange tel qu’il est à son état initial risque de se « déséquilibrer » en s’appauvrissant de sa partie glycolée ou « alcool ». Le solvant peut perdre ainsi de son efficacité.
Les solvants alternatifs étant sur le marché depuis quelques temps, le CTTN a souhaité, en complément de cette précédente analyse (encadré ci-contre), étudier l’évolution de la proportion des mélanges (solvants alternatifs multi-composés : hydrocarbure et éther de propylène glycol) au fur et à mesure des cycles de nettoyage.
En fonction des opportunités d’observation qui lui ont été offertes, il a pu s’intéresser à l’évolution de tels solvants dans 4 pressings différents.
Les solvants employés par ces pressings sont :
1) Un mélange à base d’hydrocarbure avec un alcool modifié (2 pressings A et B concernés par l’étude).
2) Un second consistant en un mélange entre un hydrocarbure et un premier éther de propylène glycol (pressing C).
3) Un troisième, différent du second mais de même principe, avec un éther de propylène glycol (Pressing D).
Solvant Analysé | Modèle machine de nettoyage à sec / capacité | Durée moyenne du cycle | Nombre de cycle réalisé depuis mise en service | Fréquence nettoyage séparateur/Type séparateur | Périodicité ajout solvant ou rééquilibrage | Remarque de l’exploitant |
1.A | ILSA Multiflex 320N 16 kg | 78 min | 394 | Manuellement 1 fois/mois | Solvant NEUF 1 fois/mois | Aucun constat particulier |
1.B | ILSA Multiflex 320N 16 kg | 70 min | 3155 | Manuellement 1 fois/mois | Solvant NEUF 1 fois/mois | Constats d’auréoles après 24 à 30 mois d’utilisation |
2.C | ILSA Multiflex 320N 16 kg | 66 min | 7549 | Manuellement 1 fois/mois | Solvant NEUF 1 fois/mois | Constats d’auréoles après 6 mois d’utilisation |
3.D | FIRBIMATIC F15ASLT2 14,5 kg | 70 min | 4534 | 1 fois/an technicien SAV | Solvant NEUF 1 fois/mois | Aucun constat particulier |
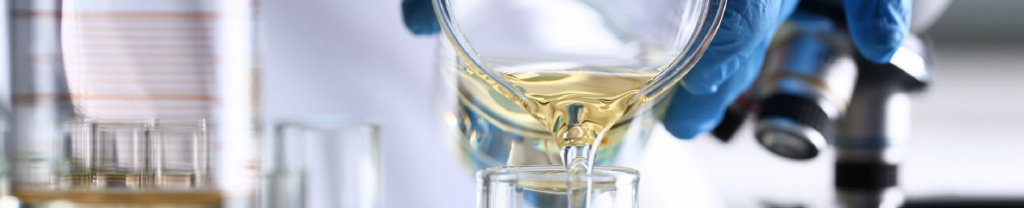
En parallèle, le CTTN a effectué des prélèvements d’eau de contact et de solvants à partir des machines concernées, au terme d’un temps de fonctionnement connu de chacune d’elles. Ces derniers ont été analysés et comparés avec les mêmes solvants neufs dans leur conditionnement d’origine et jamais utilisés en machine.
Les analyses physico-chimiques réalisées ont permis, pour chacune des installations, de déterminer la teneur en solvant des eaux de contact et la proportion des mélanges, en neuf et a près le temps d’utilisation indiqué.
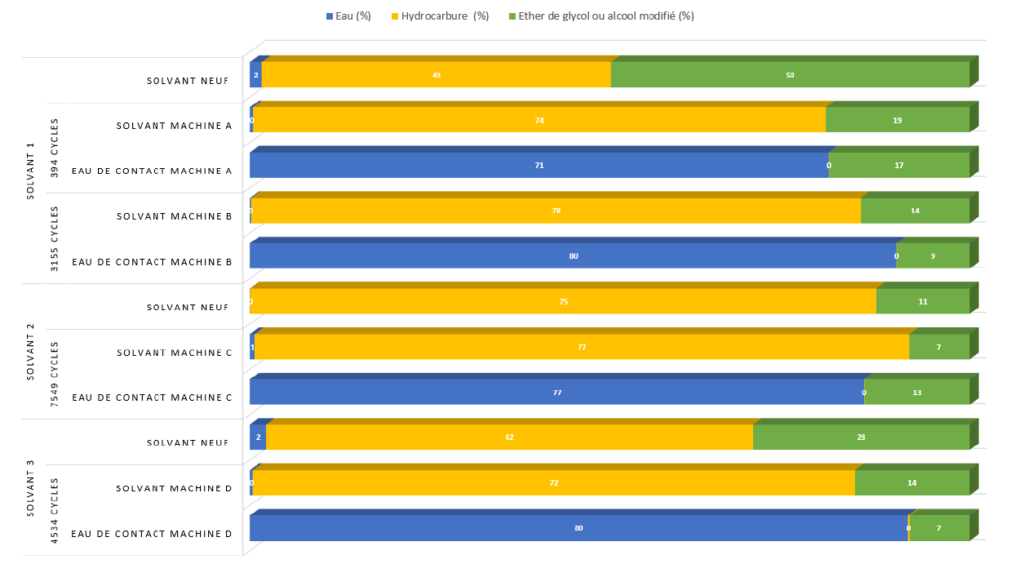
Observations :
• Les résultats d’analyse montrent bien la miscibilité relativement forte de l’alcool modifié et des éthers de propylène glycol avec l’eau. Leurs proportions se situent en effet entre 7% et 20% du volume d’eau de contact prélevé.
• Une baisse du composé alcool modifié ou éther de propylène glycol d’au moins 36 % du taux initial, pour chacun des solvants prélevés après usage.
• Les solvants qui ont subi un plus grand nombre de cycles de nettoyage marquent une tendance à perdre davantage lesdits composés en mélange (cf : Cas 1.A et 1.B pour un même solvant, par exemple)
• Le solvant 1 subit un plus fort déséquilibrage dans le temps.
• Le solvant 3 subit un fort déséquilibrage également, légèrement moindre, sachant que le prélèvement de solvant en machine a été fait avant l’introduction d’un solvant de rééquilibrage, tel que prévu pour celui-ci par son fabricant (précisément pour préserver la proportion du mélange). D’où l’importance de procéder à ce rééquilibrage.
• Le solvant 2 donne ici la variation la plus faible, sachant qu’à l’état initial, il présentait la proportion la plus réduite d’éther de propylène glycol et ce, de façon inattendue.
Considérant les différences d’activité (nombre de cycles), entre autres, réalisés par chacune des
installations avant prélèvements, ainsi que les résultats obtenus, il apparaît toutefois délicat de comparer ces données entre elles.
Il faudrait bien sûr élargir l’étude, idéalement, si les possibilités se présentaient. On observe néanmoins
qu’au fil des cycles de nettoyage, ces solvants s’appauvrissent et perdent de leur efficacité. Cette perte
se traduit notamment ici par l’apparition d’auréoles, signalée par les exploitants.
Les écarts de variation s’expliquent sans nul doute par des différences entre les molécules utilisées, selon les fabricants. Elles sont issues d’une famille de composés très étendue, qui offre un certain choix pour cette application.
Les pratiques des exploitants peuvent aussi expliquer ces différences. Par exemple, la distillation continue
n’est pas utilisée systématiquement par tous. Cela dit, il faut avoir conscience du phénomène et s’appliquer à ajouter du solvant neuf régulièrement ou du solvant de rééquilibrage lorsqu’il existe.
On peut aussi limiter la perte d’éther de propylène glycol en prenant soin des séparateurs pour préserver leur efficacité, par un nettoyage régulier (recommandation : mensuellement).
En adoptant un module de traitement complémentaire permettant de faire passer l’eau de contact sur un lit de sel, qui a pour effet de retenir l’eau sans retenir le solvant, la perte de solvant via les eaux de contact peut être réduite d’un facteur 10, voire davantage, pour le solvant 1. Le solvant ainsi séparé est réintroduit dans la machine.
L’efficacité de ce système n’est cependant pas vérifiée pour les 2 autres solvants multi composés, la miscibilité avec l’eau des composés employés pour les solvants 2 et 3 étant bien moindre que celle de l’alcool modifié contenu dans le solvant 1.